Basics|Precision pumping technology 4-4. Precautions for Using the Air Chamber (2/2)
Keep the Air Pressure at or Below 0.5 MPa Whenever Possible
When the air pressure exceeds 0.5 MPa, the air dissolves into the liquid very quickly, causing the air inside the air chamber to run out in short time. (If the air pressure is 1.0 MPa or above, air will run out in no time at all.)
Furthermore, when the pressure at the exit of the throttle valve is low, as when it is opened to atmospheric pressure, air in liquid saturated under 0.5 MPa will diffuse out until the liquid reaches the saturated air content under atmospheric pressure. Extra care must be taken for liquid that contains soap and similar products.
Always Use a Relief Valve
When using an air chamber, there is no reason not to use a relief valve. (Generally, a relief valve should also be adopted for normal usage.)
Theoretically, a diaphragm pump raises the pressure infinitely by the function of the check valve. And, the most fragile part of the system will break first. In the case of a diaphragm pump, the diaphragm, which is made of rubber, is most likely to break first.
However, in the case of a plunger pump, which does not have a rubber part, the pump is extremely robust, and the most likely part to break first is the air chamber.
The energy of compressed air is quite high. Think of a balloon for example. Even a balloon, made of a flexible rubber film, produces a powerful impact when it bursts. If an air chamber made of plastic or metal bursts in a single moment, it is by its nature an explosion. (Fig. 1)
In this case, the level of impact is not a matter of improving the strength of the air chamber by replacing a plastic chamber with a metal one. Rather, since metal air chambers can also burst when under high pressure, these can be more dangerous.
The idea of increasing the strength of the air chamber by increasing the thickness of the metal wall is out of the question. The cost will increase, and even more importantly another part of the system will break instead of the air chamber.
Considering the above, you can see how important a relief valve safety feature is in a pump system.
- *Liquid discharged from a relief valve is generally returned to the original tank. However, in cases where this method cannot be applied due to the nature of the liquid or other reasons, use a hydraulic diaphragm pump fitted with a relief valve, or a hydraulic double diaphragm pump. These pumps release the oil inside the pump if abnormal pressure is detected in the system, and never discharge the chemical outside.
Air Chambers Cannot Be Used With Liquids Affected by Air
In water treatment, a deoxidizer may be used to remove the oxygen dissolved in the liquid. For example, sodium sulfite (Na2SO3) reacts with the dissolved oxygen (O2) as described below and turns into stable sodium sulfate.
2Na2SO3 + O2 -> 2Na2SO4
If this Na2SO3 is transferred using a diaphragm pump along with an air chamber to reduce pulsation, what would happen?
Even when Na2SO3 is necessary in the boiler as shown in Fig. 2, most of it has turned into Na2SO4 inside the air chamber, creating an inefficient condition. It becomes meaningless to use Na2SO3. Another example is a food manufacturing process (e.g. dairy products) where product value can be significantly degraded by oxidation or alteration by the product coming into contact with air (oxygen). Naturally, you cannot use an air chamber in such cases.
Throttle Valve Needs Re-Adjustment Every Time the Pump's Discharge Volume Is Changed
We already looked at how the throttle valve needs to be re-adjusted when an air chamber is used to reduce pulsation in a previous section (4-2. Working Principle of Air Chambers). To put it the other way around, when the pump's discharge volume changes, the balance between the discharge volume and the resistance from the throttle valve is inevitably lost, resulting in stronger pulsation. Therefore, the throttle valve must be re-adjusted so as to reduce the pulsation.
Delayed Discharge Occurs When the Pump Is Started and Liquid Drips When the Pump Is Stopped
Fitting the end of the discharge-side pipe with a solenoid valve can resolve the problems described in (1) and (2) above, but if the solenoid valve wears out or if dirt gets caught in it, its sealing may deteriorate, which can lead to serious problems.
The corrosion resistance, pressure resistance, service life, and explosion protection specifications of the solenoid valve must also be considered.
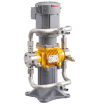
TACMINA's Smoothflow Pump can provide continuous metered transfer without an air chamber. No risk of chemical splattering from air chamber bursting. No more delayed discharge at pump start-up or liquid leaks when pump is stopped.
More...