Basics|Precision pumping technology 8-1. Compression Ratio
Considering the principle of positive displacement, you can presume that air (gas) entering the pump head can have serious consequences. Let's take a look at the impact of air on the diaphragm pump.
Compression Ratio
Imagine an injection syringe once again.
When liquid is sucked into the syringe, if air enters the syringe as shown in Fig. 1 (2), not only does it remain in the syringe as shown in (3)' when the diaphragm is completely pushed in, but it prevents us from knowing how much liquid has been injected. To avoid these problems, you remove the air completely while holding the injection syringe facing up as shown in (3) in order to ensure an accurate injection amount.
The part where air still remains after completely pushing in the diaphragm as shown in (3)' is called a dead space. When you say a pump has a good compression ratio, it normally refers to having a small dead space vis-à-vis the volume of the contracting and expanding diaphragm cavities.
Here, if the total volume inside the pump head is V and the actual contracted/expanded volume inside the diaphragm is V', the compression ratio can be expressed by the following equation:
Compression ratio = V / (V - V')
The illustration for this calculation is shown in Fig. 2 below.
For example, if the total volume of the pump head is 100 mL, and the contracted/expanded volume is 90 mL, the compression ratio will be as follows:
Compression ratio = 100 / (100 - 90) = 10
This indicates that liquid is compressed to 1/10 its natural volume. The dead space at that time is 100 - 90 = 10 mL.
Compression Ratio of Diaphragm Pump
The compression ratio of a diaphragm pump can be considered the same way as that of an injection syringe. (Fig. 3)
So, what is the difference between an injection syringe and a diaphragm pump?
A diaphragm pump has two openings, specifically, a suction port and a discharge port for liquid, and thus the dead space is larger. Moreover, because the diaphragm does not hit the front wall of the pump head, the dead space is even more expansive. For this reason, the compression ratio of a diaphragm pump is worse than that of an injection syringe.
It is possible to create a design in which the diaphragm hits the front wall when it moves completely forward, but depending on the dimensional tolerance of the parts, the diaphragm may make contact with the front wall while it is still in motion. This may result in damage to the drive unit bearing or a motor burn-out. As such, care is taken to ensure some space exists between the innermost position of the diaphragm (top dead center) and the front wall of the pump head.
Nevertheless, this space does not need to be larger proportionally to the capacity of the pump. This implies that because the compression ratio is greater in pumps with larger capacity, a gas lock is less likely to occur. Conversely, smaller pumps are more prone to gas locks.
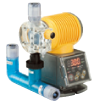
TACMINA's DCLPW Series, dedicated to sodium hypochlorite injection, offers a perfect solution to injection problems with its double block mechanism that prevents gas locks.
More...