Basics|Precision pumping technology 1-2. Diaphragm Pump: Frequently Occurring Problem
Differences Between Diaphragm and Centrifugal Pumps
"In a pH control application using a control valve, after replacing the centrifugal pump used as a chemical injection pump with a diaphragm pump, the diaphragm pump and piping got damaged."
This problem is a good example that represents the differences in the characteristics of the centrifugal pump and diaphragm pump.
Let's look at the differences.
Centrifugal Pump
For example, let's consider a case of controlling the neutralization (pH 7) of waste water of pH 14.
- When a 20 mA signal indicating pH 14 is sent from the pH meter, the control valve opens completely, allowing maximum flow rate from the centrifugal pump.
- As the pH value drop, the signal current from the pH meter also gradually decreases, which causes the aperture of the control valve to get smaller. As a result, with the increase of pressure loss, the transfer liquid backflows from the gap between the casing of the centrifugal pump and the stirrer blade, which reduces the discharge volume.
- When the pH value reaches 7, the signal is 4 mA, closing the control valve completely. Then the discharge volume and the backflow amount balance out, consequently reducing the flow rate to zero.
Therefore, the pressure does not rise beyond the pump lift even when the pump is operating. This protects the pump and piping from breakage (bursting) in most cases. (Damage caused by water hammer or other forces is another issue.)
Diaphragm Pump (Replacing Only the Centrifugal Pump and Using the Same Line)
(Relief valve not installed)
- When a 20 mA signal indicating pH 14 is sent from the pH meter, the control valve opens completely.
This has very little impact on the diaphragm pump. (Only valve pressure loss) - As the pH value drop, the signal current from the pH meter also gradually decreases, which causes the aperture of the control valve to get smaller.
The working is the same as the centrifugal pump up to this point...
But it is significantly different from here. Remember how the check valve works?
"Once liquid enters the cylinder (pump head), it is forced out of the discharge side by the working of the check valve."
Therefore, however large the force holding the ball check valve may be, the pressure inside the cylinder keeps increasing until some part breaks.
This means that a fixed amount of liquid is discharged from the diaphragm pump regardless of the narrowing of the control valve aperture. Enormous pressure is generated when this happens, and may result in serious consequences to the pump and piping.
In conclusion, you can say that trying to control the discharge volume from a diaphragm pump with a control valve is a big mistake.
You cannot change the discharge volume of a diaphragm pump using a control valve.
As we have seen here, pressure loss increases as liquid passes the control valve.
The waveform of liquid discharge from a diaphragm pump generally resembles a sine curve as shown in Fig. 3. This indicates that the discharge speed (flow velocity: instantaneous flow) is not constant, with the liquid cyclically flowing faster and slower.
Looking at the figures, the highest flow velocity is π times (approx. 3.14 times) the average flow velocity.
The pressure loss at the control valve (nozzle part) increases roughly in inverse proportion to the square of the diameter of the aperture. For instance, halving the diameter of the pipe will increase the pressure loss 4 times.
For this reason, controlling the discharge volume of a diaphragm pump using a control valve can build up pressure and pose a huge risk.
Controlling the Discharge Volume of a Diaphragm Pump
How can we control the discharge volume without using a control valve?
The answer is:
"To remove the control valve and apply a mechanism that controls the rotations per minute (stroke speed) of the diaphragm pump."
This approach increases or decreases the total discharge volume (for example, discharge volume per minute) as a result of changing the stroke speed while maintaining the discharge amount per stroke of the diaphragm pump.
As such, signals from the pH meter are transmitted to the following control systems:
- Inverter-driven control system
- Thyristor-driven control system
- CVT-driven control system
Which system to adopt depends on the liquid quality, purpose of control, budget, and other factors.
Fig. 4 below shows an example using an inverter-driven control system.
If a centrifugal pump is to be replaced by a diaphragm pump at a site, keep in mind the above characteristics to successfully make the changeover.
On the other hand, if there is an incident where the diaphragm of the diaphragm pump breaks or the discharge-side pipe bursts, it is necessary to check during repair whether a control valve is used in the piping.
The lift and maximum allowable pressure of a diaphragm pump
What it means when the lift (head of liquid) of a centrifugal pump is 30 meters, is that the pump has the ability to carry water 30 meters upward. Therefore, water blasts out with a pressure (energy) equivalent to about 0.3 MPa from the discharge port of the centrifugal pump.
In contrast, when a diaphragm pump has a rated maximum pressure of 0.3 MPa, it means that a pressure over 0.3 MPa may cause the pump to break--it does not mean that water at the discharge port of the pump has a pressure of 0.3 MPa.
The pressure applied to a diaphragm pump depends on the pressure at the discharge side (including piping resistance).
This is to say, the pressure applied to the pump is 0.01 MPa when the discharge-side pressure is 0.01 MPa, and 10 MPa when the discharge-side pressure is 10 MPa.
Customarily, the term "lift" may be used to refer to the maximum allowable pressure of a diaphragm pump, but remember that the meaning is different from the lift of a centrifugal pump.
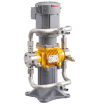
TACMINA's Smoothflow Pump is the only diaphragm pump that ensures continuous metered supply with no pulsation. Liquid can be transferred with constant flow without being affected by pressure fluctuations.
More...